Innovators lead the charge on industrial energy efficiency
Developing and demonstrating technology innovations can be challenging, but doing so during a global pandemic is additionally tough. Paul McKinney, Programme Manager for the BEIS Industrial Energy Efficiency Accelerator at the Carbon Trust, looks at the achievements and tenacity of the innovators who are playing a leading role in decarbonising the industrial sector.
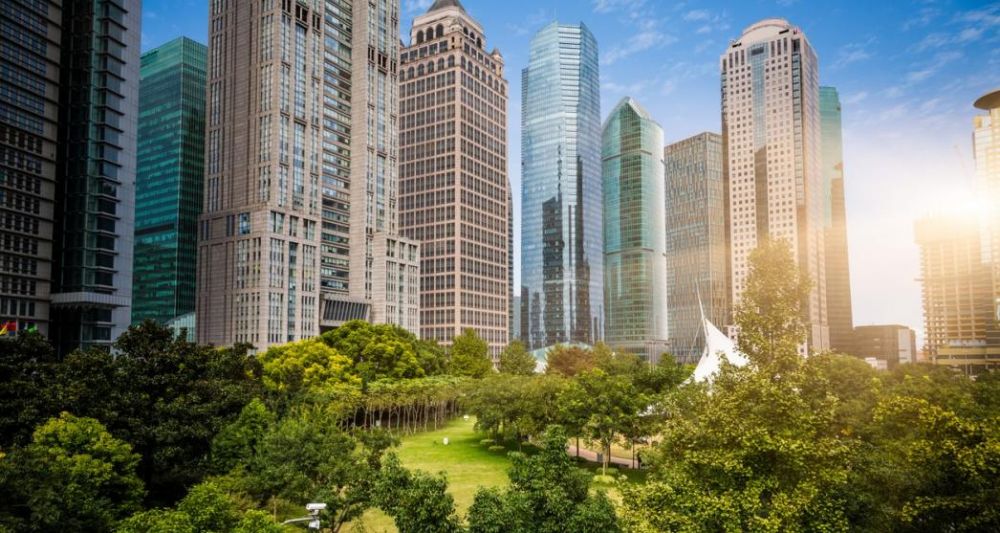
Developing and demonstrating technology innovations can be challenging, but doing so during a global pandemic is additionally tough. Paul McKinney, Programme Manager for the BEIS Industrial Energy Efficiency Accelerator at the Carbon Trust, looks at the achievements and tenacity of the innovators who are playing a leading role in decarbonising the industrial sector.
Meeting the UK’s net zero target will require unprecedented innovation across the economy and this is especially the case in traditionally energy hungry industries. As the deployment of renewable electricity and biomass sourced fuels, and plans to develop clean hydrogen accelerate, it is clear that all have a role to play in reducing, and ultimately eliminating, industrial carbon emissions. However, it has always been the case that prioritising strategies that enable companies to use less energy in the first place is usually the most cost effective solution to deploy first.
To achieve industrial energy efficiency at the scale and pace we need, we must go beyond the adoption of existing technologies and best practice. Which is why a recent UK government programme – the £10m BEIS Industrial Energy Efficiency Accelerator (IEEA) - has focused on supporting UK-based technology innovators, many of whom are SMEs, who are leading the charge to bring new solutions to market quickly.
The IEEA
The UK government has invested over £500m since 2015 through an Energy Innovation Programme to accelerate the commercialisation of innovative clean energy technologies and processes, and the IEEA is part of this investment. Managed by the Carbon Trust, and supported by engineering services company Jacobs, the IEEA is working to boost the number of innovative and step-changing energy efficiency technologies available to UK industry, by supporting the demonstration of new industrial technologies at commercial scale. Encouraging the wider uptake of these innovations will also help to strengthen the global competitiveness of UK industry in sectors including manufacturing, waste processing and data centres.
Sixteen collaborations between technology innovators and industrial energy users have been benefiting from grant funding averaging 50% of total project costs, to develop and demonstrate new technology in operational environments, that will have a transformative effect on the target industries.
One of the biggest barriers to the adoption of new technology in industry is the perceived risk of being first. With grant funding and project support to mitigate the risk, the IEEA projects aim to demonstrate that these new technologies can work on an industrial scale, and give confidence to the markets for rapid scale-up and replication. Beyond financial support, the project participants benefit from help from Jacobs to develop meaningful Measurement & Verification plans, and from Carbon Trust incubation and marketing expertise to ensure that they progress with their commercial development, as well as proving technical success.
Covid-19 disruption
However, like many, the IEEA hadn’t envisaged the challenges that this year would present to its innovators. Covid-19, as well as the terrible human cost inflicted across the planet, has upended almost every aspect of life, bringing disruption to many innovators and in many cases putting their business survival at risk.
Just as many of the IEEA projects were due to move to on-site demonstration, Covid-19 and the resultant lockdown, stopped them in their tracks. Suddenly, installing new technology to industrial processes was put very much on the back burner. Workers had to isolate or be furloughed. Supply chains dried up and, for understandable reasons, access to the industrial sites was restricted to core personnel only.
But the innovators have risen to the challenge, finding inventive and imaginative ways to ensure their businesses could continue, and keeping their projects progressing. The following are a few examples of this:
Magnomatics
Magnomatics is a high technology company based in Sheffield that is developing and manufacturing products based on its ground-breaking magnetic gear technology. It is seeking to deploy a direct drive magnetically geared motor into a waste shredder at Ellgia’s Scunthorpe waste management site. By removing the need for inefficient gearboxes and pulley systems the project will demonstrate the energy savings available from his technology operating under harsh operating conditions, including high torque, speed fluctuations and vibration in service.
When the lockdown hit, Magnomatics acted quickly to identify the potential impacts. Its biggest concern was its supply chain – some of its suppliers no longer had the capacity to meet commitments – and so it went back to the drawing board, re-designing aspects of the product so that the Magnomatics team could produce some components in house, or with alternative suppliers. The project management team was quick to re-prioritise activities and re-schedule the project when faced with delays to groundworks at the demonstration site.
The company’s designers were able to adjust to working from home, following a rapid investment in its IT network and installation of CAD-design packages and equipment at the designers’ homes. Like many, Magnomatics has faced a tough few months, but is still on track to deliver on its demonstration objectives, albeit with a few months’ delay. The key to success has been thinking ahead, undertaking regular and thorough risk reviews to identify and plan for issues before they happened, and then being very flexible in its response to keep the team working towards the end goal. The team have brought creativity to problem solving and kept working towards the project objectives, even when the original project plan was diverted.
Agritec Systems
Agritec Systems in Chesterfeld is developing an innovative low temperature animal by-product processing technology. This will enable the capture of valuable by-products as an alternative to current high temperature rendering processes. Agritec experienced the opposite problem with its supply chain to Magnomatics. A key supplier providing analytical services is also an active supplier to the NHS. Demand for the supplier’s services grew rapidly and it had to postpone work for its other customers, including Agritec. The project partners have managed to creatively reschedule their activities and have worked closely with the Carbon Trust and BEIS, to effectively restructure their activity plan.
Building back better
Covid-19 could potentially set back the implementation of new technology in industry for years to come. Capital investments made over the next two or three years will lock in energy use for the next 10-20 years or more, so it is vital that new technology is implemented within those investments in order to bring down carbon emissions cumulatively over that period.
It has, therefore, been hugely encouraging to see how some of these dynamic, flexible technology companies have overcome the additional challenges that Covid-19 has brought, ensuring that the exciting technologies they are developing will soon be demonstrated at scale and commercialised to allow widespread replication across industry.
The technologies developed through the IEEA are also perfectly placed to contribute to the UK’s green recovery.
Matrix Moulding Systems
For example, Matrix Moulding Systems (MMS) is developing a new ultrasonic flow enhancement technology for the plastics injection moulding sector. Early industrial scale trials are already showing energy savings of up 19% and significant cycle time reductions. In a traditional sector, in which average energy savings are typically 1-2% per year, it is clear that a 10-20% saving would be transformational.
MMS will be demonstrating its Soniplas technology at Barkley Plastics in Birmingham for various injection moulding configurations and a successful demonstration will highlight the potential to retrofit many of the estimated 10,000 injection moulding machines in the UK.
The current IEEA comes to an end in December next year, but we expect it to deliver a step-change in efficiency across many sectors.
We have modelled the potential cumulative carbon saving in the UK over 10 years if all the IEEA-supported technologies achieve realistic replication goals. These equate to up to 10 million tonnes of CO2, which will give industry across the UK a global competitive edge as carbon targets and market expectations become more stringent.
Ultimately, the programme will demonstrate that, with the right support, technology innovators can achieve great things and overcome extraordinary challenges.
Find out more about the BEIS Industrial Energy Efficiency Accelerator here.
Get in touch with the Carbon Trust here.