Carbon Footprint of Recycled Aluminium
Production of primary aluminium through the Hall Heroult electrolysis process is energy intensive. The carbon footprint of primary aluminium is thus highly dependent on the source of electricity used.
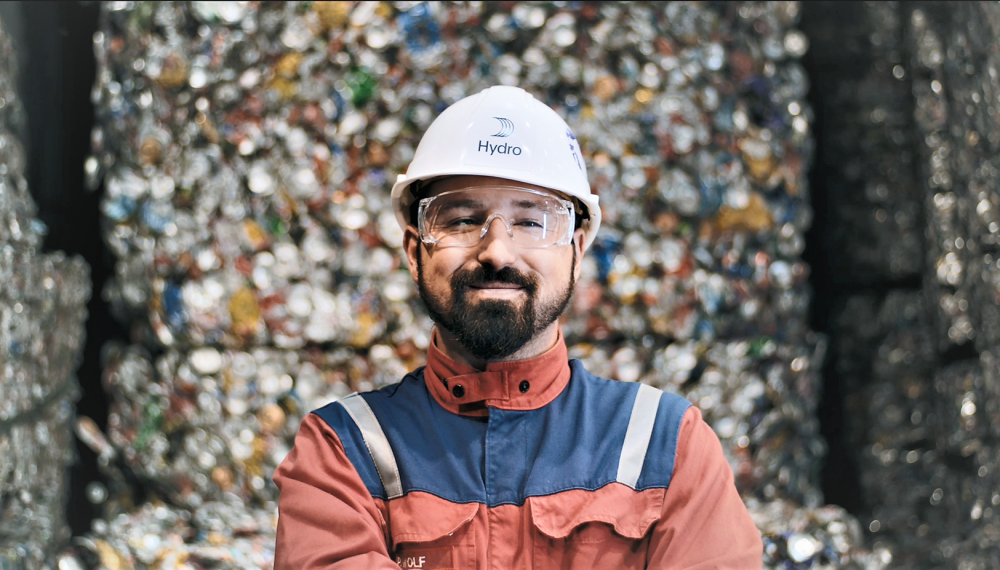
Background
Production of primary aluminium through the Hall Heroult electrolysis process is energy intensive. The carbon footprint of primary aluminium is thus highly dependent on the source of electricity used. As a result, the carbon footprint of primary aluminium varies between less than 4 tons CO2-equivalents per ton aluminium in hydropower-based regions to more than 20 tons CO2-equivalents per ton aluminium in coal power-based regions. The recycling process of aluminium, however, requires a lot less energy than primary aluminium production, and thus emits less CO2 - approximately 0.5 tons CO2-equivalents per ton aluminium.
The carbon footprint of recycled aluminium
With the low carbon footprint of the recycling process for aluminium, the question arises: what is the carbon footprint of the recycled aluminium itself? It is then necessary to look at the history of the recycled aluminium. Post-consumer scrap is defined as aluminium scrap that comes from products which have fulfilled the purpose for which they where produced. This scrap might range from aluminium cans with a lifetime of about 60 days to buildings with a lifetime of more than 50 years. When this scrap is recycled, it starts its second life as a recycled product, with no carbon footprint history attached to it. As a result, post-consumer scrap has a carbon footprint of about 0.5 tons CO2 per ton aluminium. This results from scrap collection, transport, sorting and remelting.
The situation is quite different for process scrap. Process scrap arises during processing of aluminium products, such as e.g. extruded profiles or rolled foil. During processing of aluminium, typically between 20 and 30 per cent ends up as process scrap. This process scrap is of high value, and the recycling rate of this scrap is close to 100 per cent. However, the process scrap has never fulfilled its purpose as a product, and thus carries the carbon footprint of the original primary aluminium from which it is produced. This means that the carbon footprint of recycled process scrap is not 0.5 tons CO2 per ton aluminium, but the carbon footprint of the original primary aluminium PLUS 0.5 tons CO2 per ton aluminium. Some companies claim that the carbon footprint of process scrap is equal to the carbon footprint of post-consumer scrap. Such an approach would then equalize hydropower-based aluminium and coal-based aluminium as soon as the metal is processed. This approach would lead to “greenwashing”, would favor industrial inefficiencies, and is not supported by Hydro.
Hydro’s position
Hydro calculates carbon footprint of aluminium by modelling physical realities as closely as possible. This is done by following acknowledged LCA methodologies, as outlined in ISO 14040-44. We don’t equalize process scrap and post-consumer scrap in our calculations, but regard process scrap as primary aluminium that has to be remelted once more. As a result, the carbon footprint of recycled process scrap is equal to or even higher than the carbon footprint of primary aluminium. Post-consumer scrap, on the other hand, has fulfilled its purpose in its first life cycle, is starting its second life cycle, and has thus no historical carbon footprint attached to it.
ISO 14021 definitions
Pre-consumer material: Material diverted from the waste stream during a manufacturing process. Excluded is reutilization of materials such as rework, regrind or scrap generated in a process and capable of being reclaimed within the same process that generated it.
Post-consumer material: Material generated by households or by commercial, industrial and institutional facilities in their role as end-users of the product which can no longer be used for its intended purpose. This includes returns of material from the distribution chain.
Visit Hydro.com/Recycling for more information.
Follow Hydro on LinkedIn here to receive more information about recycling of aluminium.