PepsiCo saved $80 million by using less water
PepsiCo’s Frito-Lay snacks facility in Casa Grande, Arizona was the first food manufacturing site which obtained the LEED EB Gold certification, in 2009 from the US Green Building Council, and it has a “near net zero” footprint
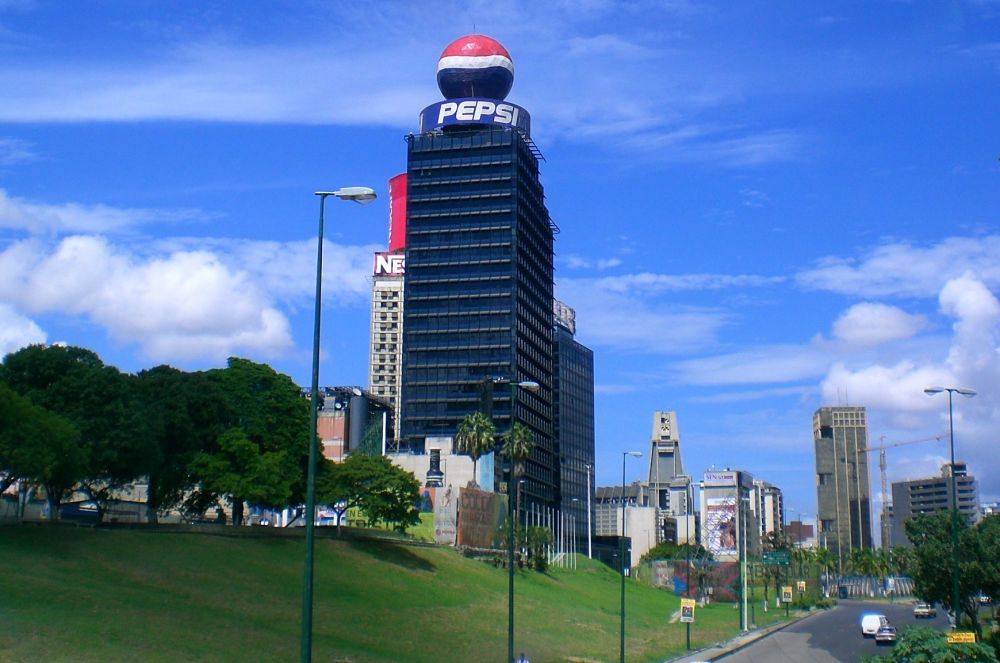
PepsiCo’s Frito-Lay snacks facility in Casa Grande, Arizona was the first food manufacturing site which obtained the LEED EB Gold certification, in 2009 from the US Green Building Council, and it has a “near net zero” footprint.
The facility treats and recycles around 648,000 gallons of process water every day, for rinse and wash water and landscape irrigation, which means 75 per cent of process water is recycled, reducing the water use of the facility by 100 million gallons per year.
The water conservation target has allowed the company to save $80 million in utility bills notably and other expenses between 2011 and 2015.
PepsiCo has reduced its operational water use per unit of production by 26 per cent last year compared to 2006 – exceeding its 20 per cent target, the company has announced last Monday.
PepsiCo alongside with Kellogg have been ranked food and beverage industry’s leaders in water efficiency by Lux Research.
The food and beverage giant’s environmental sustainability programme also involves energy, packaging and waste reduction initiatives, and it has saved the company $600 million during the last five years.
As part of the water conservation programme and thanks to its charity – the PepsiCo Foundation, 9 million people have been provided with safe water since 2006.
PepsiCo’s Al Halvorsen, senior director environmental sustainability global operations, said: “As a global food and beverage company, water is the lifeblood of our business and the many communities we serve... Conserving water across our global enterprise can have a huge impact on our communities and our planet. From a business perspective, these efforts help us lower our operating costs. By doing more with less, we are able to increase our agricultural yields, strengthen our water infrastructure and deliver cost savings.”
The success of the company in increasing efficiencies is due to the implementation of new technologies, including monitoring and fixing leaks, recycling and reusing water, and treating wastewater with cost-optimised biological treatments, capacitive deionization and forward osmosis
The company has also launched diverse community education campaigns and initiatives to help locals have access to safe water in several developing countries.